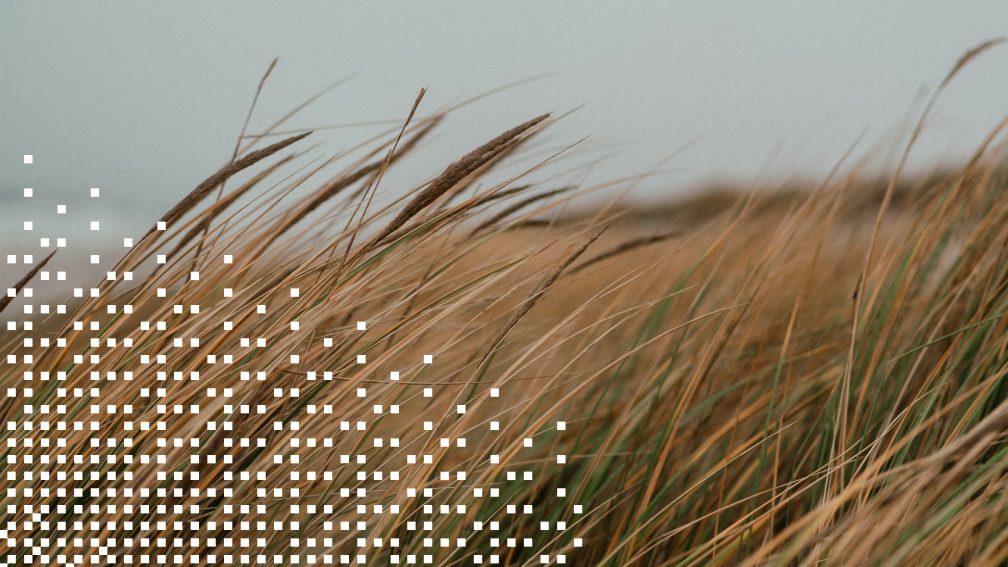
February 18, 2021 • 12 min read
Manufacturing Risk: 4 Areas of Digital Investment for 2021
As we approach one year since the beginning of lockdowns in North America, Deloitte projections (based on the Oxford Economic Model) show annual manufacturing GDP growth levels continuing to decline, with a forecast of -5.4% in 2021, compared to a forecast of -3.7% in 2020. Although the trajectory of decline is slowing, manufacturers are bracing for the future by focusing on the assets, people, and capabilities required in a post-pandemic world.
Executives and experts alike acknowledge the need for embracing technology to address the ongoing challenges of an unpredictable manufacturing risk environment in 2021. The manufacturing industry has been particularly vulnerable to pandemic-related risks, as the majority of its workforce consists of on-site employees who cannot perform their responsibilities remotely. A recent survey of over 350 manufacturing executives found that 76% intend to increase their investments in digital initiatives, in addition to piloting and implementing more Industry 4.0 technologies (Industry 4.0 refers to the fourth industrial revolution, which affects every manufacturing domain and comprises advanced manufacturing technologies that capture, optimize, and deploy data.). In particular, such digital transformation will be crucial for creating greater connectivity among global supply chains, and improving the quality and efficiency of manufacturing processes at the factory level. This article will explore four areas of digital investment that can help manufacturers build resiliency, efficiency, and cost-savings into their systems and operations. These areas are:
- Risk Management Technology
- Digital Twin Technology
- Digital Supply Networks
- Talent Ecosystems
Risk Management Technology
While many lament the unpredictability of the 2020 pandemic and its lasting effects on society, others are quick to point out that the risk of a global pandemic was not a black swan event, but one that scientists, economists, flu and disease experts, and more have been predicting for decades. Building the possibility of “disruption” into your business operations is necessary as we move forward from the lessons of this past year. Yet, compared to other impacted industries such as Healthcare and Energy/Utilities, Manufacturing industry groups indicate a lower likelihood of investing in more risk management capabilities in 2021, as revealed in a recent Protiviti and NC State ERM initiative report. This statistic pales against the importance of a mature enterprise risk management (ERM) program to an organization’s resilience in a volatile risk environment, and its survival over time.
A continuous risk monitoring program that provides visibility into your risks is the key that unlocks preparedness and resiliency in the face of disruption. The bedrock of such a mature ERM program is technology; specifically, a platform that provides real-time visibility into an organization’s top risks, as these risks will inevitably change in priority as external events unfold. One of the best pre-emptive initiatives to navigating future disruptions is investing in a cloud-based solution that will serve as the single source of truth for your organization’s top risks, allowing you to track and manage your risks as they change in real time. Moreover, having a centralized platform for all your risks can also help organizations streamline risk data and risk management activities, eliminate duplicate risk management efforts, and strengthen cross-functional visibility and coordination. This is beneficial for maximizing collaborative efforts between internal audit, risk management, and compliance teams. Most importantly, a continuous risk monitoring program, anchored by a cutting-edge technological solution, is the underlying foundation for a year-round risk management mindset. Organizations with clear visibility into their changing risks are more prepared for disruptions than those who are not continuously monitoring their risks. As a result, they will be more likely to quickly and effectively pivot during times of crisis when timely responses are crucial to survival.
“Visibility is likely to become the most critical capability for manufacturers in the coming months.”
Digital Twin Technology
Another area of digital investment for manufacturers is digital twin technology. Almost a quarter (24%) of manufacturing executives who plan to pilot and implement more Industry 4.0 technologies believe digital twin technology will be the most important technology, tied with augmented workforce efficiencies. In manufacturing, a digital twin is a representation or blueprint of a physical product, component, production process, or physical production environment. Digital twins can help manufacturers prepare for future unknown events by essentially simulating performance in the real world without needing to actually sacrifice any physical resources. The benefit of having a library of digital twins representing the key elements of manufacturing operations is its ability to help manufacturers forecast and see weak areas in their operations and supply chain without having to take any physical action. According to Deloitte’s 2021 Manufacturing Industry Outlook, manufacturers who invest in digitizing their product plans, processes, and environments could potentially mitigate the historic losses in productivity and output that many faced during the onset of the pandemic.
Digital Supply Networks
While manufacturers have historically focused on how to make their supply chains more cost efficient, one takeaway from the pandemic has been the importance of supply chain agility in the face of disruptions such as trade risks and global pandemics. In addition to expanding options for where products are sourced and made, forward-thinking organizations are also transitioning from traditionally linear supply chains to more interconnected and dynamic systems known as Digital Supply Networks (DSNs).
A Digital Supply Network uses technology solutions to integrate real-time data from demand and supply planners to drive the physical act of production and distribution. A functional DSN is composed of a digital stack of applications that suit a manufacturer’s business objectives. This hub integrates and synchronizes layers of data from multiple sources, including products, customers, suppliers, and aftermarket support, providing enhanced visibility into the extended supplier network that enables better-informed decision-making for manufacturers. This is because a DSN empowers each supply node to become more capable and connected, allowing information to transcend the traditional communication path, where information travels linearly and data tend to be siloed in separate nodes. DSNs also improve flexibility across a global supply network by enabling faster use-case appropriate responses to new events like sudden shifts in demand or supply. Ultimately, the enhanced visibility of a DSN allows manufacturers to develop an inventory strategy based on data and insights. In order to begin transforming a supply chain into a Digital Supply Network, it is important to start small and truly understand what is driving the need for differentiation before beginning to build your digital ecosystem.
Talent Ecosystems
As manufacturing companies invest in digital initiatives to stay competitive and resilient, they will also need to invest in their workforces. For example, a company that is investing in building DSNs and Digital Twins will also need to consider the skills, training programs, and resources required to manage these new technologies. This is echoed in a recent survey by Deloitte that found 28% of manufacturing executives believe the greatest challenge to managing their workforce is upskilling their employee base to keep pace with the digitization of other aspects of their business. In anticipation of this challenge, some manufacturers are focusing on building talent ecosystems. A recent study by the Manufacturers Alliance for Productivity and Innovation (MAPI) and Deloitte found that over 80% of manufacturers surveyed believe talent ecosystems are critical to their competitiveness, and 41% have already started forming partnerships to develop robust ecosystems.
A talent ecosystem is a network of external partners that work with a manufacturer to strengthen its talent pipeline. Talent ecosystems are a viable solution as increasing numbers of manufacturers shift to more hybrid production and non-production processes, requiring greater agility and cross-functionality of their existing workforces. External partners can include employment service providers, academia, apprenticeship programs, technology councils, government programs, technical training centers or schools, and gig economy associations. These partners factor into the talent ecosystem in various ways, from providing training programs to reskill existing talent or train-to-hire programs with a job offer upon successful completion of the program. The benefit of the ecosystem is that these various partners purposefully coordinate with and among one another in service of their shared business objectives with the manufacturer. Not to mention, ecosystems help facilitate faster overall digital transformation in businesses, which can have a direct impact on financial performance.
The Future of Manufacturing
As manufacturers look to create greater resiliency and flexibility in their systems and operations, embracing effective technology will be critical to helping them accomplish their goals, from reimagining global supply chains to building the workforces and factories of the future. Simultaneously, it is also important to learn from the past lessons of 2020 as manufacturers look ahead to the future. Rather than focusing on siloed efforts to improve productivity and cost-efficiency, manufacturers should ask themselves how they can drive greater visibility and cross-functional collaboration internally, as well as how to coordinate more closely with their peers, external partners, and the public sector to forge the relationships necessary for fueling and sustaining rapid digital transformation.
You may also like to read
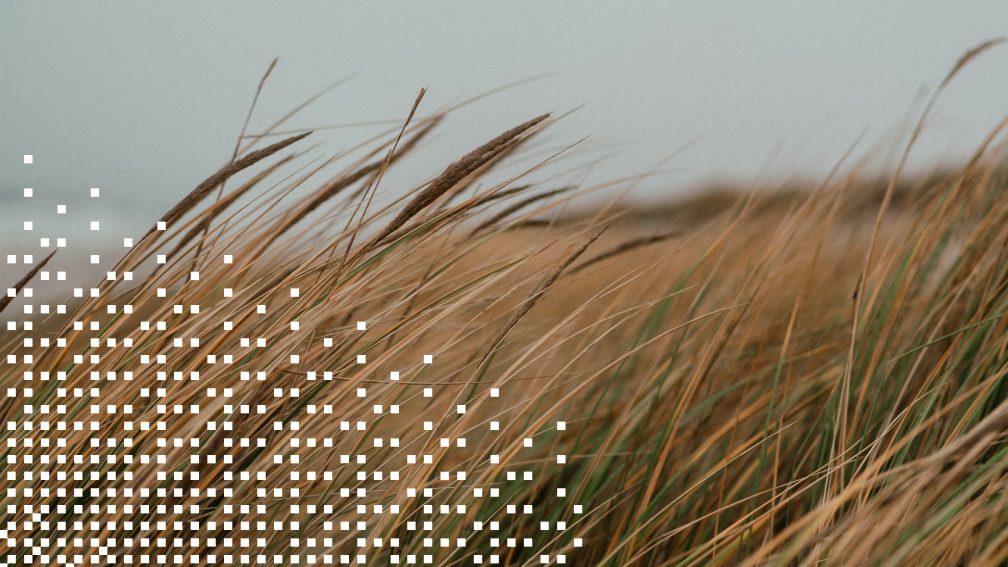

Effective planning in permacrisis requires unified, collaborative risk leadership
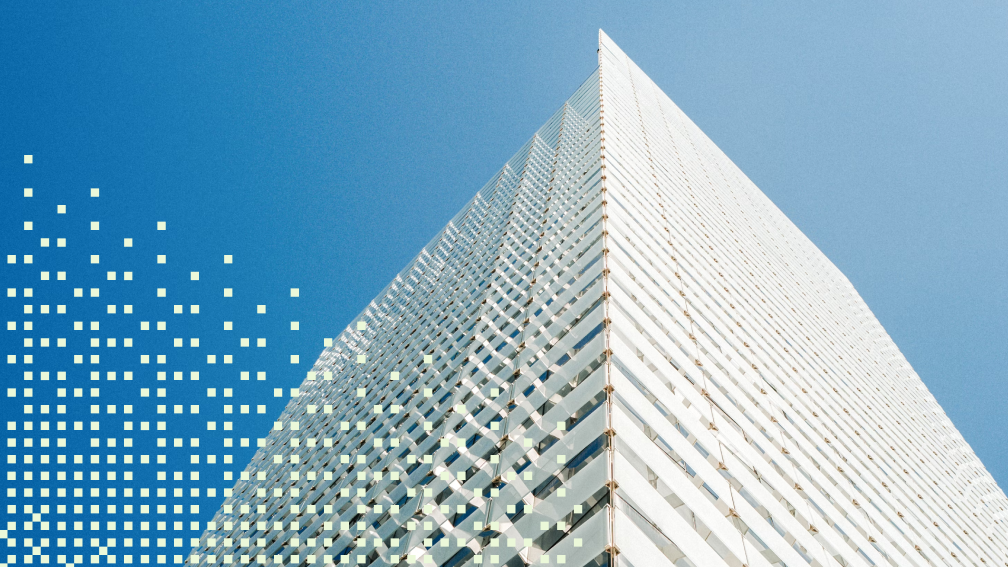
Fraud triangle: A practical guide for internal audit teams
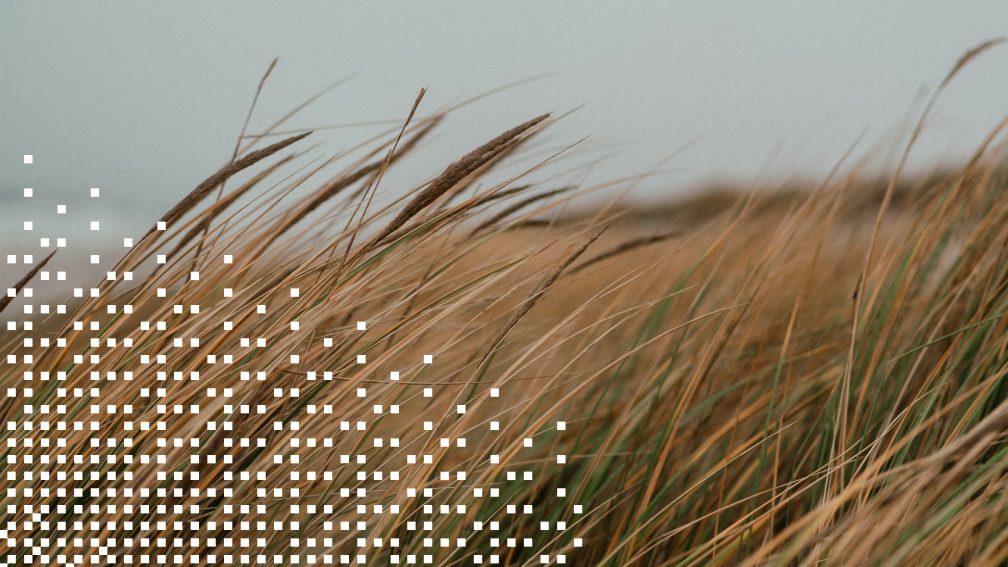
HR audit process: A practical guide to streamline compliance and risk

Effective planning in permacrisis requires unified, collaborative risk leadership
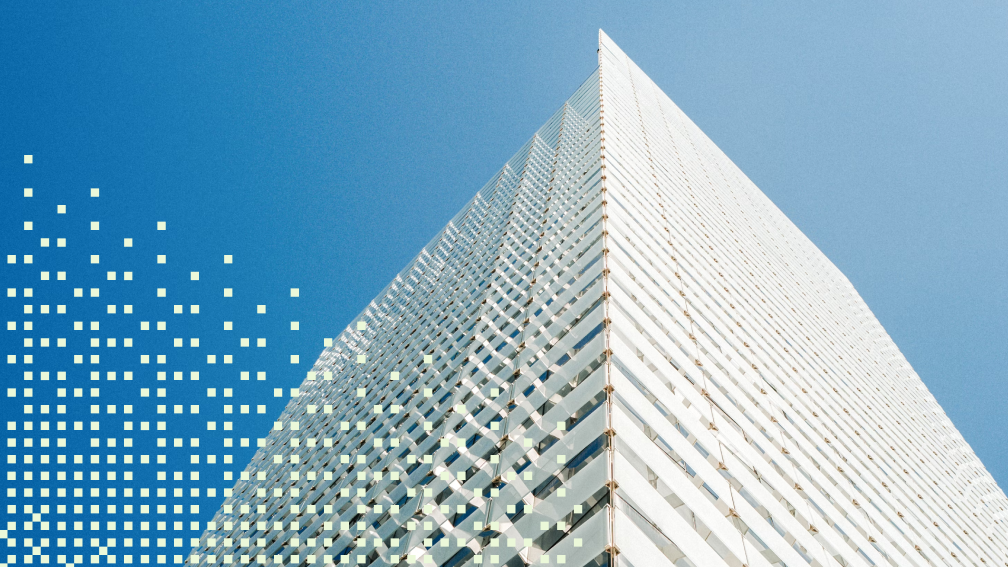
Fraud triangle: A practical guide for internal audit teams
Discover why industry leaders choose AuditBoard
SCHEDULE A DEMO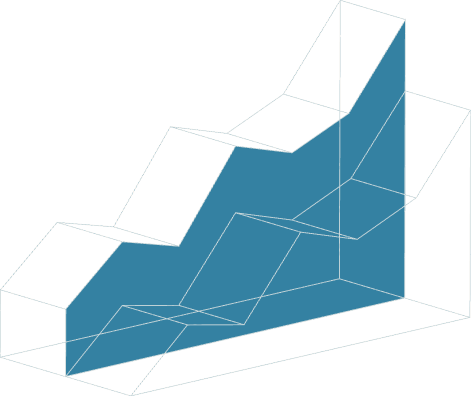
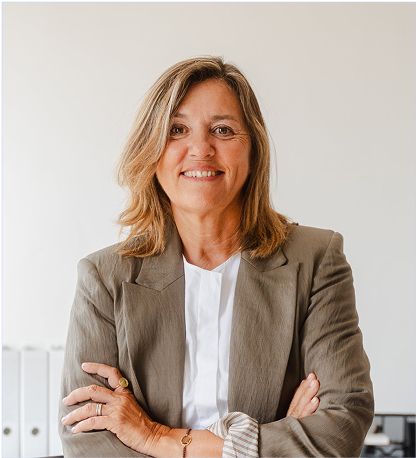