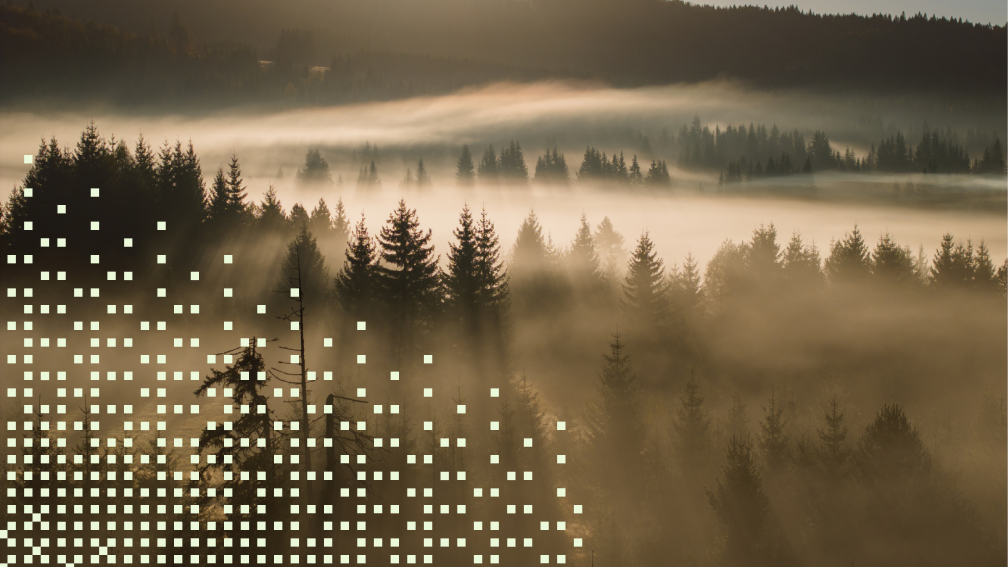
January 12, 2022 • 7 min read
Assessing Weak Links in the Supply Chain
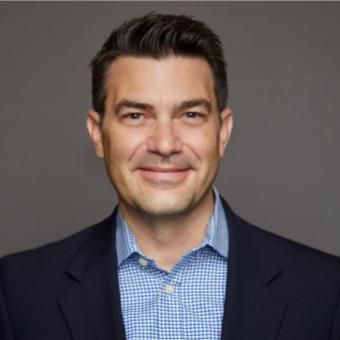
Scott Madenburg
At the pandemic’s start, most audit departments quickly realized the need for more frequent risk assessments. The risk landscape has continued to shift and change over the past two years in unexpected ways, making the need for frequent assessment even more critical. Due to ripple effects, supply chains are the latest atypical risk spiking on enterprise risk management assessments across industries as the effects of the pandemic continue impacting businesses. Read on to learn five top supply chain risks to consider in your risk assessment, and one approach to organizing your supply chain assessment to give management the insight needed to make critical business decisions.
5 Top Supply Chain Risks Today
On the global level, several significant supply chain issues have been highlighted in the media. Congestion at the world’s largest ports highlighted weaknesses in logistics, while microchip shortages impacted automobile, gaming, and computer manufacturing. As consumers, we felt localized supply chain issues in different ways. In the US, while we had an abundance of TV streaming content, we experienced unforeseen shortages in toilet paper, swimming pool chlorine, take-out containers, home office equipment, bicycles, and the list goes on. With this in mind, here are five of the top supply chain risks you should consider in your risk assessment:
1. Lost Revenue
Home gaming products like the Sony PlayStation (PS5) experienced increased demand, with more people seeking home entertainment options. However, the microchip shortage made it impossible to meet the demand leading to lost revenue. To put this in perspective, the PS4 sold 116 million units with a standard price of $399 (over $46 billion). The PS5 has sold out at 13 million units at $499 (just $6.5 billion). If we assume the same volume despite the increased cost, over $52 billion in lost revenue that competitors are doing all they can to take away from Sony.
2. New Competition
Competitors, both existing and new market entrants, are devising alternatives to lure away customers. At the start of the work from home movement, Zoom was perfectly poised to provide a video conferencing option that met the consumer’s requirements. The gains made by Zoom (317% revenue increase from 2019 to 2020) triggered a battle between Cisco, Microsoft, Facebook, and Google to create video conferencing alternatives to draw individuals and companies away from Zoom.
3. Inflation
Prices are going up for raw materials like wood, steel, and aluminum. The US inflation rate rose 6.8% in 2021, the highest increase since 1982. Travel costs are up for cars, fuel, flights, and hotels. Restaurant supplies and ingredient costs for meat, dairy, and produce are all on the rise. The prices are passed on to the consumer with expenses going up, but increased prices typically lead to decreased sales. Balancing the cost to provide the goods and services being sold versus the price consumers are willing to bear can make or break a company.
4. Reputational Damage and Great Resignation
Online retailers, grocery stores, and healthcare facilities saw significant increased demand which took a toll on their employees and their reputation. Frontline workers publicly complained about working conditions that included unrealistic expectations and unsafe practices. This also led to increased resignations and the worker shortages that are now hindering manufacturing and distribution across all industries, further impacting the supply chain. Do you see the domino effect?
5. Fraud Exposure
The global demand for personal protective equipment (PPE) skyrocketed during the pandemic, and the situation was primed for fraud. Profiteers were quick to hoard supplies, sell fake goods, and price gouge desperate hospitals and individuals who depended on the products. Others gathered used gloves and masks and resold soiled and contaminated products as new, which cannot be used, costing the company money and endangering those who rely on the equipment. Performing a targeted fraud risk assessment will give you insights into specific vulnerabilities in your environment.
How Can You Organize a Supply Chain Assessment?
One approach to organizing a supply chain risk assessment is to apply the top five risks listed above (and any other risks you have identified, like cybersecurity) to the components of your supply chain management process. These would usually include processes such as:
- Vendor Selection and Management
- Product Design and Manufacturing
- Demand Management and Projection
- Inventory Management
- Order Fulfillment – Warehousing
- Order Fulfillment – Delivery
- Handling Product Returns
What Comes Next?
Supply chain issues are unlikely to be resolved anytime soon. The complexities of a global economy are more likely to produce unanticipated risks and new problems as the ripple effects of the pandemic are felt over the next decade. Understanding the risks in your supply chain will give management the chance to make critical business decisions. Armed with the knowledge of your supply chain risk, management will be able to plan for shifts in product availability, react to logistical changes, and avoid bottlenecks that could stretch your supply chain to the breaking point.
About the authors
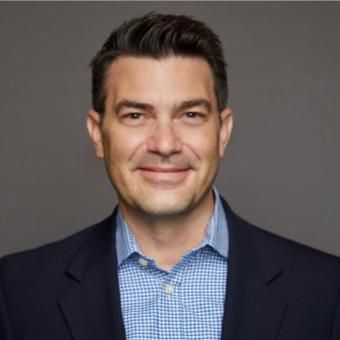
Scott Madenburg, CIA, CISA, CRMA, is the founder of ARCHybrid, where he serves as a market advisor, consultant, and trainer, guiding organizations and professionals in transforming their audit, risk, and compliance functions to enhance efficiency, strengthen controls, and address emerging threats. Connect with Scott on LinkedIn.
You may also like to read
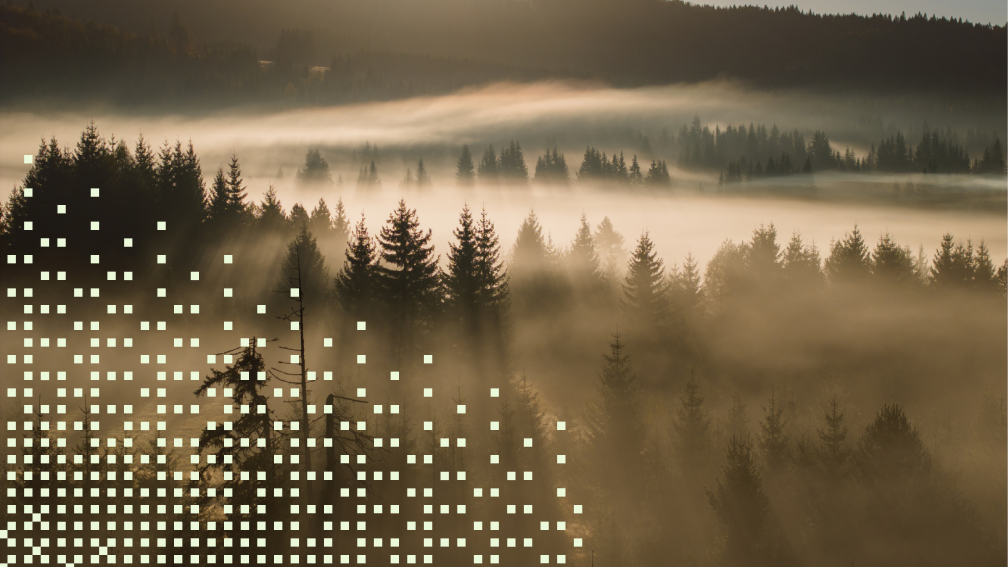
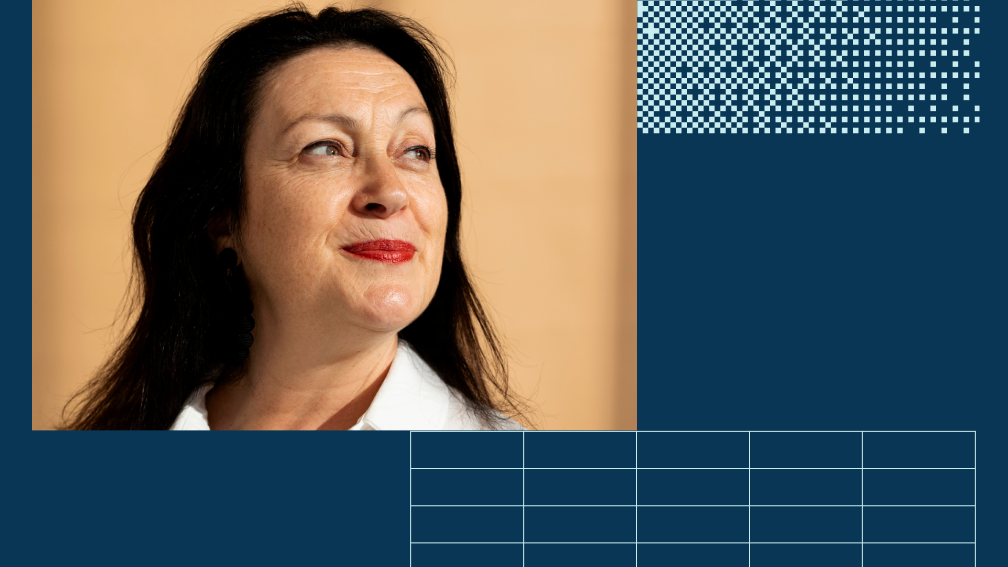
Internal audit in local government: Time to lead, not linger
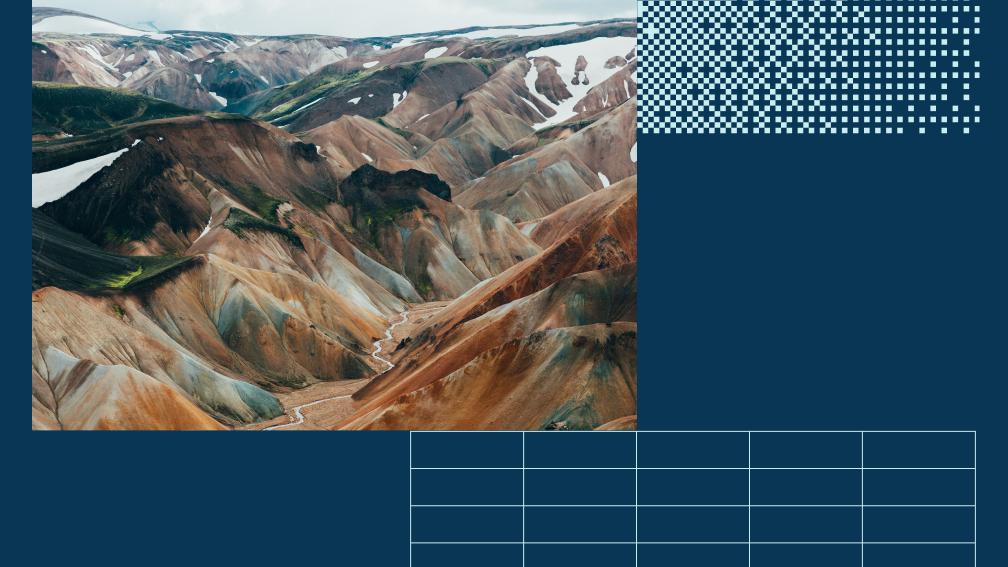
4 key ways technology can help internal audit deliver more value to organisations
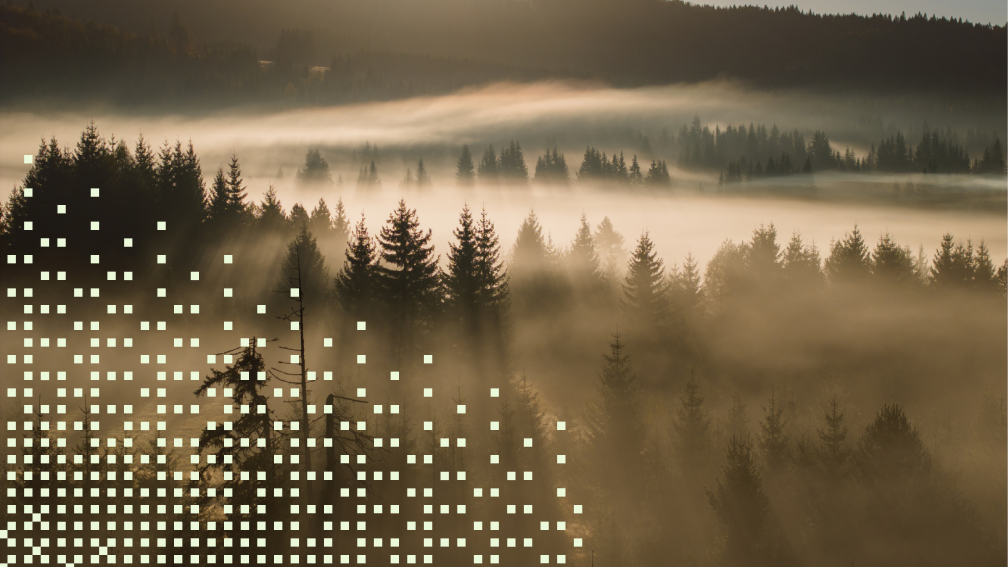
Embracing real-time risk assessment: A practitioner’s guide for internal audit teams in 2026
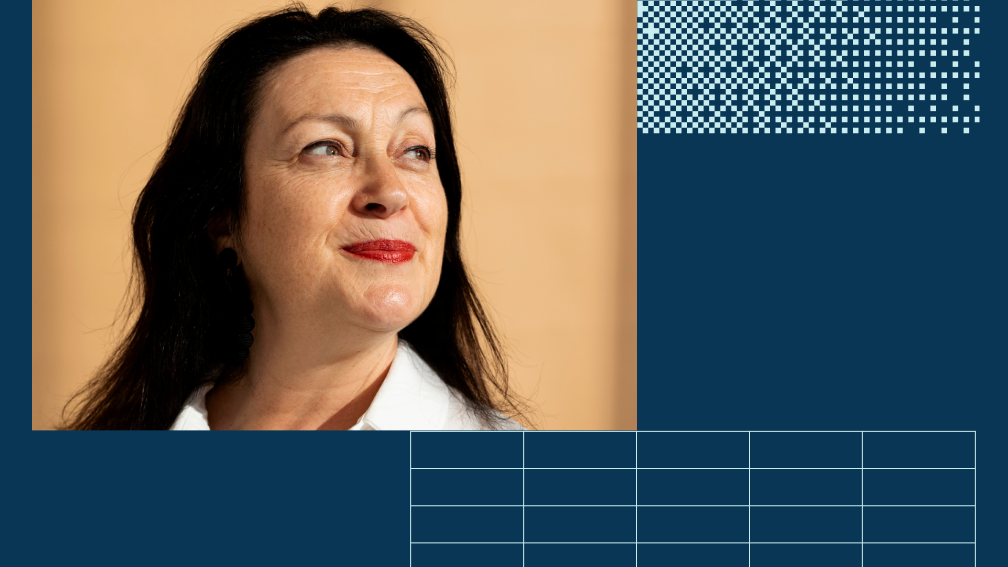
Internal audit in local government: Time to lead, not linger
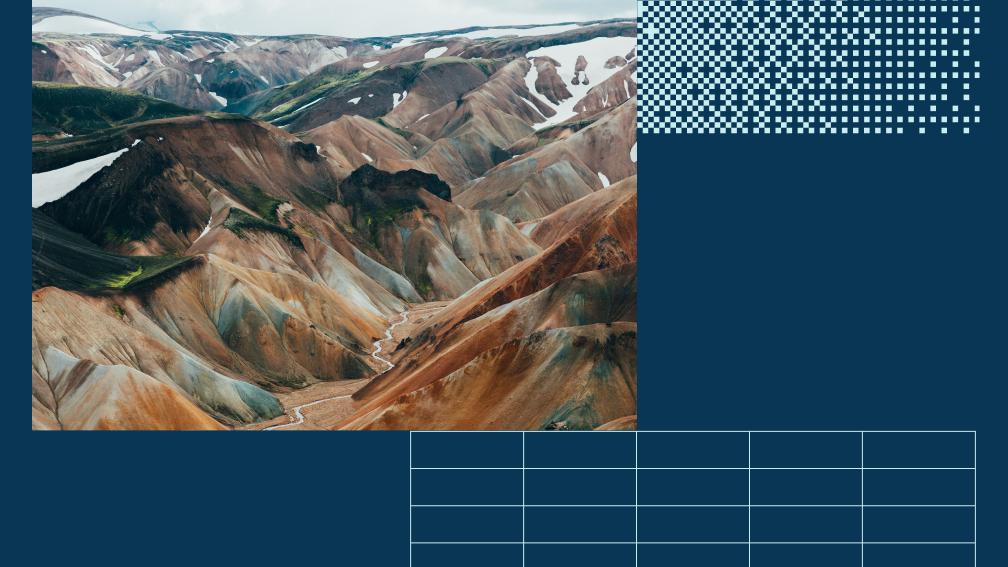
4 key ways technology can help internal audit deliver more value to organisations
Discover why industry leaders choose AuditBoard
SCHEDULE A DEMO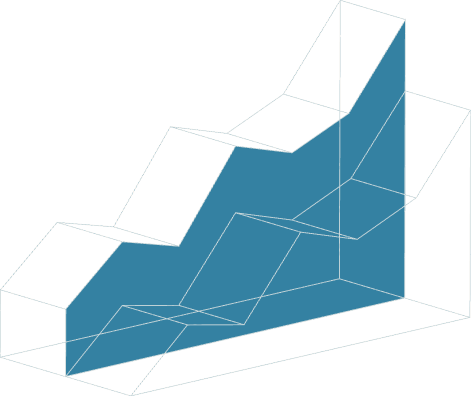
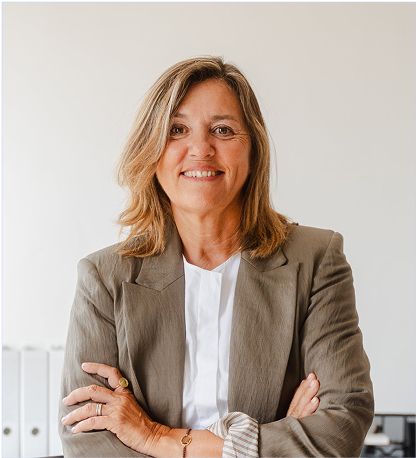